
Oil Spill Clean-Up

Oil Spill Clean-Up
Waterbender - Oil & Ballast Technology employs innovative thermodynamic processes to
effectively purify various types of water pollution, specifically oil and oil
products, including ballast water contaminated with chemical reagents and sediments
from tankers. It is also capable of fully treating water generated during
hydraulic fracturing for shale gas extraction, enabling its reuse in a closed
water cycle, as well as recycling of acidic tar and other oil product waste
mixed with water, acids, and other substances.
The innovative Waterbender - Oil & Ballast Technology equipment utilizes phase transition technology to separate water from dissolved salts, petroleum products, chemical residues, as well as natural and artificial pollutants, such as sand and soil.
When treating ballast water, the system produces
the following output materials:
- Highly purified fresh water suitable for storage, industrial processes, or safe discharge into natural water bodies
- Separated oil and oil products with low emulsification
- Solid sediment composed of chemicals mixed with sea salt
When purifying hydraulic fracturing water, the output can include:
- Large volumes of fresh water
- Proppants (small particles like sand or ceramics) used to create cracks in shale rock during the fracturing process
- Chemical additives, including surfactants, biocides, pH control agents, and other chemicals, as well as traces of crack control agents
During the purification process, solid particles
are separated and removed, while fresh water and petroleum products are
directed to tanks or pipelines for further use.
Waterbender - Oil & Ballast Technology is highly efficient and unmatched worldwide,
eliminating the need for complex and costly equipment. The equipment is
housed in 40-foot containers, allowing for mobile installation on trolleys,
ships, or railway platforms.
The system has exceptionally low energy
consumption and can utilize solar or wind energy. It does not require
consumables, chemicals, reagents, inhibitors, coagulants, filters, cathodes,
anodes, etc. With a processing capacity of up to 75 tons of input mixture per
day, the equipment can operate 24/7/365 with minimal staffing requirements
and no need for highly qualified personnel. Productivity can be increased by
using multiple sets of 40-foot containers with linearly increasing capacity.
With proper thermal insulation, the equipment is suitable for operation in
different climatic zones.
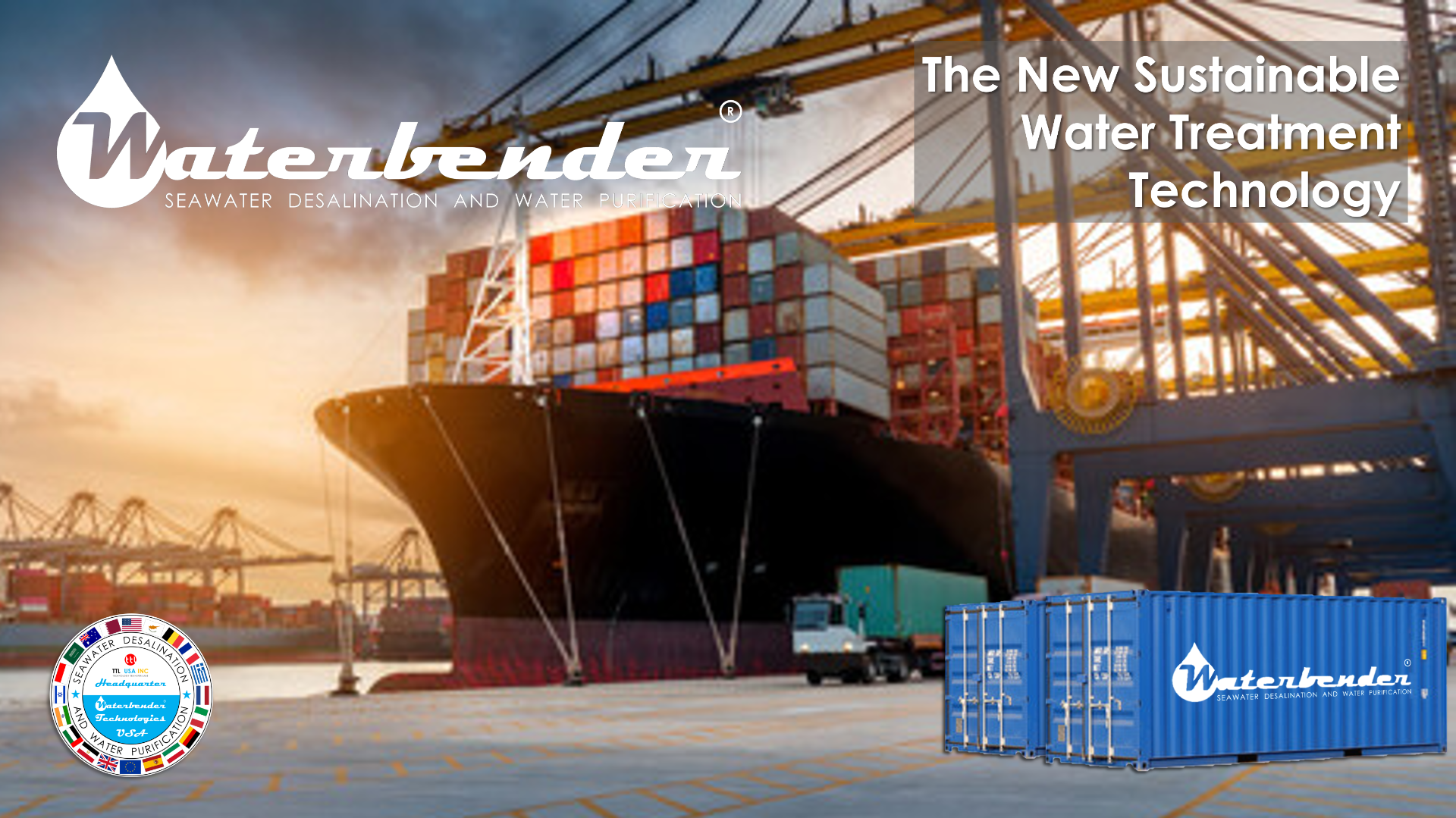
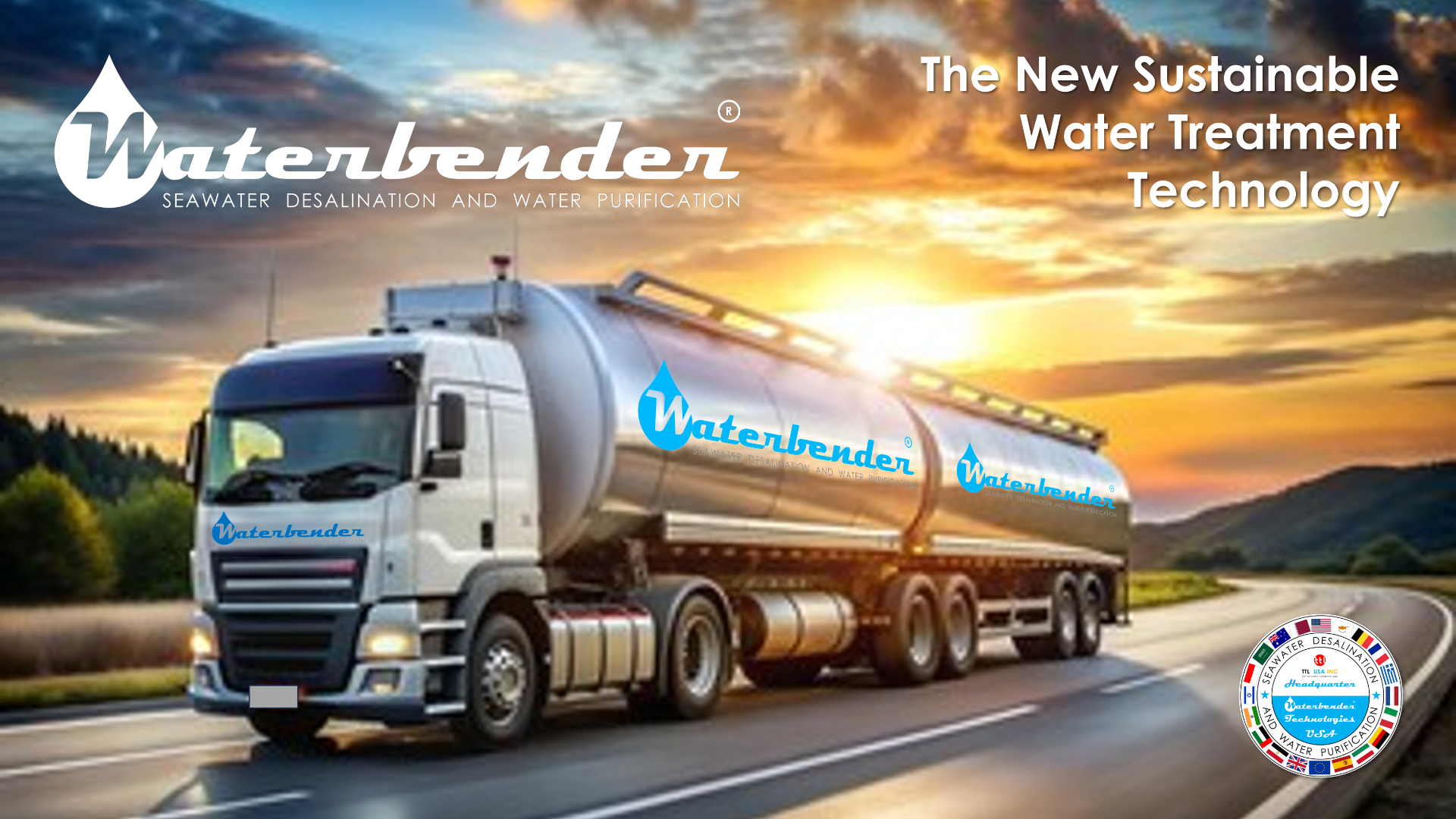
If you are interested in the technology or have any questions, please contact us!
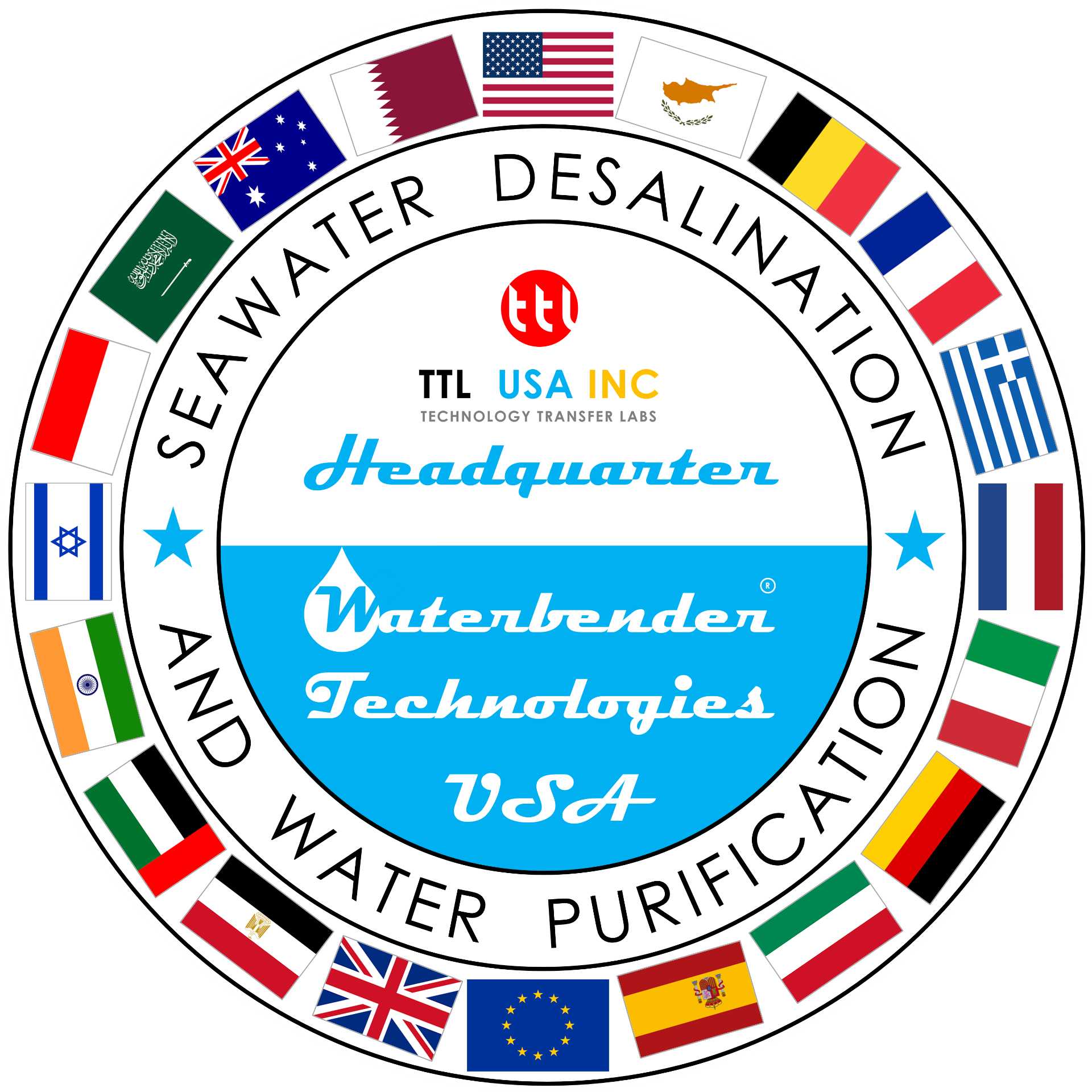
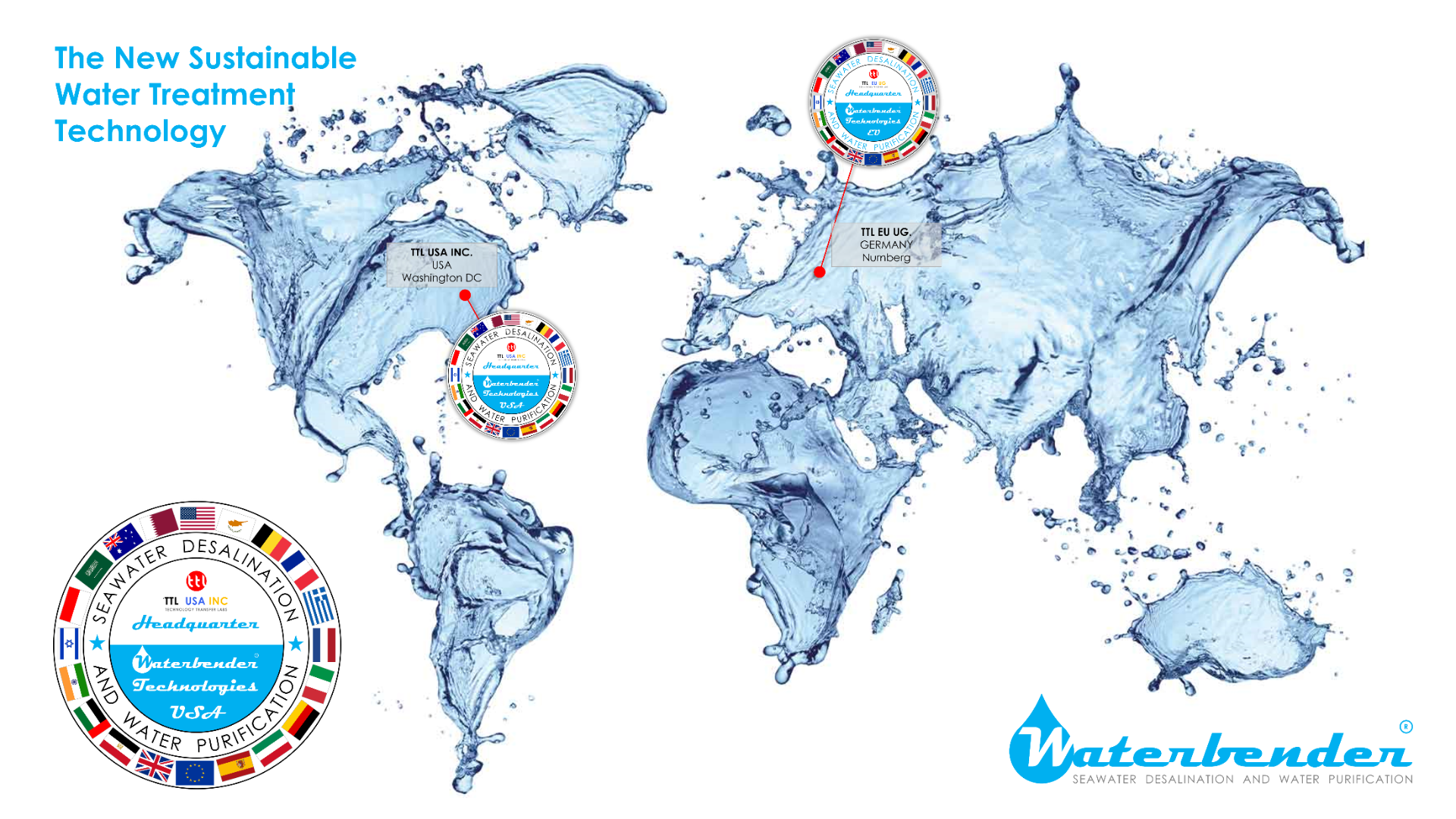